Smaller meat processors face backlogs as coronavirus continues to shutter large slaughterhouses
Small meat processors across the US and Canada report months-long bottlenecks as farmers search for abattoirs to process backlogged livestock.In an in-depth analysis by PJ Huffstutter and Rod Nickel from Reuters, small-scale slaughter operations report spikes in numbers as COVID-19 outbreaks at major US and Canadian meat plants force farmers and consumers to seek alternatives to a crucial supply chain link.
Inside the small-scale Iowa abattoir Stanhope Locker and Market, owner Shaunna Zanker yawns with exhaustion as she listens to yet another farmer asking her to slaughter his pigs.
"I'm so sorry, but we're booked through March of next year," Zanker said on the phone. "How about next June?"
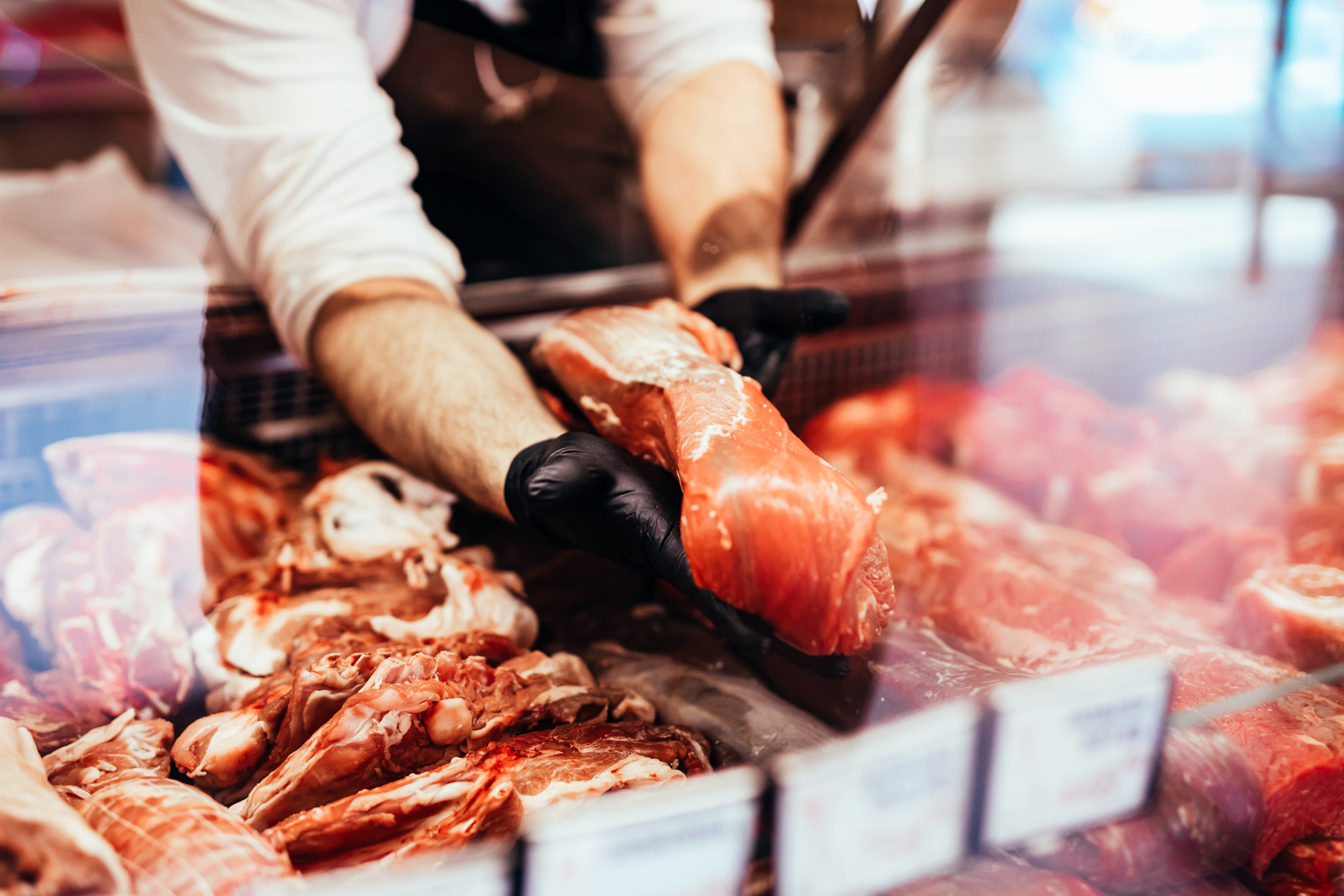
Since 1946, this Stanhope, Iowa, shop – one of 1,500 independent American slaughterhouses - has processed a few farm animals from local farms each week and sold cuts of beef and pork to the public.
Now the family-owned business and others like it are overwhelmed and are forced to turn away farmers. Since COVID-19 outbreaks among abattoir workers have left large meat processors closed or at reduced capacity, there aren’t enough places to slaughter thousands of cattle and pigs. The reduction in capacity has also left store shelves with little or no meat in major exporting countries that would otherwise have healthy supplies.
In the US, small-scale processing plants represent a miniscule portion of the market – nearly 80 percent of US beef is produced by four large companies. Economists estimate that around 1 percent of American hogs are processed and small-scale meat lockers.
The consumer rush for meat is straining supplies at TL Keller Meats in Litchfield, Ohio, and forced them for the first time ever to ration sales: Five pounds (2.3 kg) of ground beef per person and two packs of burger patties per family.
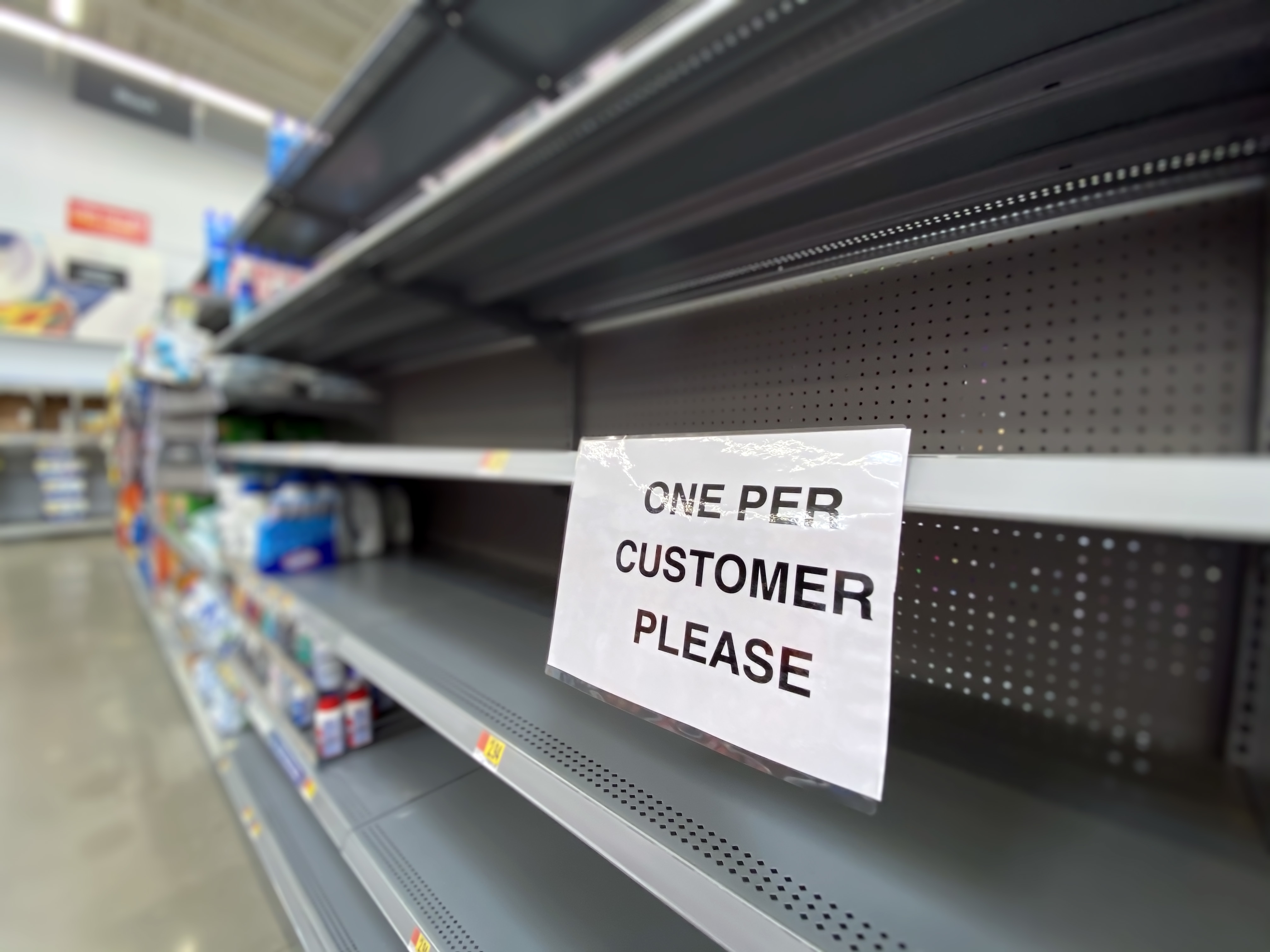
Owner Tom Keller and his 23 employees are processing as fast as they can. In March, they slaughtered 104 cattle, twice the rate a year earlier.
"People are going mad trying to fill their freezers," Keller said after putting in a 13-hour day.
A new spate of panic buying
Alberta, Canada’s main cattle-producing province, is struggling to deal with reduced production capacity at the country’s two main beef plants, owned by Cargill Inc and JBS SA.
Cattle at the feedlot stage are being turned away from the big plants as the backlog of supplies steadily grows.
In response, some farmers are calling Marc Lustenberger, owner of the Meat Chop abattoir near Penhold, Alberta, who already has a brisk business cutting meat for farmers to sell directly to consumers.
“There's lots of panic buying," Lustenberger said. "Looks like it's not going to stop anytime soon."
In March and April, Alberta's Red Deer Lake Meats slaughtered twice as many pigs and cattle as it normally does. The provincial agriculture department called Red Deer butcher Darrel Barrett to ask him to pick up some of the slack from the two-week closure of Cargill's plant.
"Which is absurd, with Cargill slaughtering 4,500 head a day," Barrett said. "We're lucky if we do 20 a week."
Like other Alberta butchers, Barrett is also busy cutting meat for farms that are suddenly doing booming sales directly to consumers.
One customer, rancher Ben Campbell of Black Diamond, Alberta, pre-sold 10,800 pounds (4,900 kg) of grass-fed beef in two months, one-third more than he sold all of 2019.
Small ranchers like Tim Hoven, who runs an organic beef farm near Eckville, Alberta, have years-long relationships with small butchers that are now seeing massive demand. Neighbours, used to delivering to the big plants, are left with cattle that have nowhere to go.
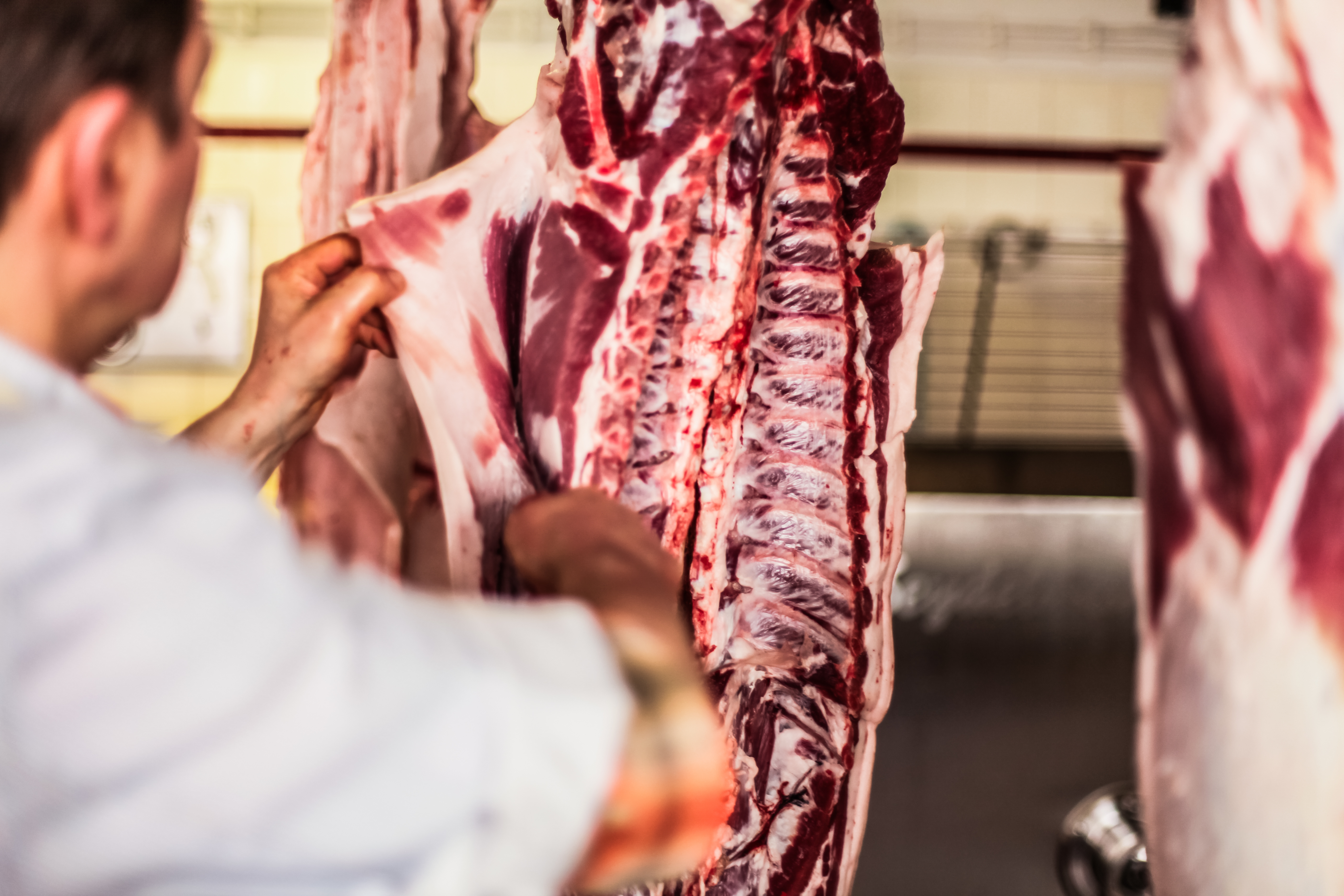
"They're in a tough spot because they're small and they're at the bottom of the list to get that kill spot at these big plants," said Hoven, whose meat sales have tripled.
"They can't get that spot at the small plants" either.
The "new way to buy food"
At Uniontown, Alabama-based BDA Farm, sales have jumped more than 800 percent in two months, said partner Allen Williams.
"Initially it was panic buying, but it has gone far beyond that now," Williams said. "They're discovering an entirely new way to buy food and they're discovering it's pretty dad-gum convenient."
"We're selling out of absolutely everything, every single week. But we're running into a choke point - we can't get it all processed."
Back in Iowa, Zanker hangs up the phone. It's the tenth farmer to call that day.
Next, a woman calls asking if Stanhope Locker and Market has meat for sale. They do. The woman lives two hours away. Others have driven further, Zanker said.
"I had one person call, telling me they had gotten a hog for free," Zanker said. "I told them, 'There's nowhere to take them. Congratulations, you now have a pet.'"