Feed-mill biosecurity critical to reducing disease transmission
Feed and feed ingredients are generating a lot of interest as possible vectors in transmitting swine diseases, and based on evidence from the 2013 porcine epidemic diarrhoea virus (PEDv) outbreak, it is justified - at least to a degree.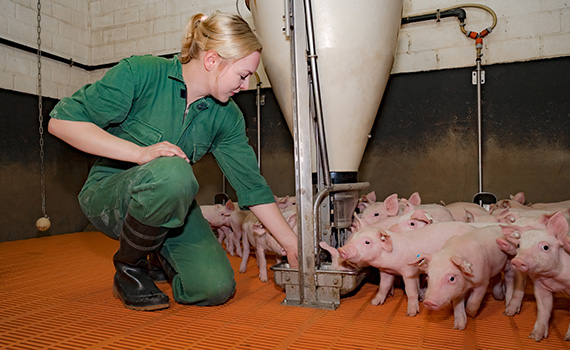
“Feed is just one of many risks,” said Cassandra Jones, PhD, associate professor in animal sciences and industry at Kansas State University (KSU). “However, the way that we manufacture and deliver feed increases the likelihood that, if contaminated, the feed will elicit disease.”
Jones is one of the members of KSU’s feed-safety research team, which includes veterinarians, swine nutritionists and feed scientists.
Certainly, the confirmed link between feed and PEDv, combined with the global African swine fever (ASF) scare, are reasons enough to sit up and take notice. Using models, research has shown that both of those viruses can survive the trans-oceanic trip to the US in numerous feed ingredients. Notably, surrogate viruses for foot-and-mouth disease and Chinese pseudorabies had similar survivability rates to ASF virus, with classical swine fever virus being less hardy, based on preliminary knowledge..
Research also found that one reason PEDv spread so quickly through the US feed supply was the low infectious dose - just 5.6 x 10^1TCID50 per gram in feed. For perspective, Jones told Pig Health Today, that equates to 1 gram of faeces from an acutely PEDv-infected pig being capable of contaminating 500 tonnes of feed.
Earlier this year, research at KSU’s Biosecurity Research Institute Level III Laboratory confirmed that ASF virus is able to infect pigs through feed and liquid - and the risk climbs with repeated exposure. For example, at a minimum virus dose of 10^4TCID50, a pig with one feed exposure would have a 25 percent likelihood of infection, but after 30 exposures, that likelihood would climb to nearly 100 percent.
“Based on this data, it’s possible that even low levels of ASF virus may cause infectivity through feed,” Jones said. “The bad news is that feed-based exposure is not a single risk event; it’s repeated and can reach many pigs and farms quickly.”
A change in mindset
There is a lot to dissect when swine disease questions filter back to the feed, ingredients and/or the mill. In general, most people within the pork and feed-manufacturing sectors still view swine diets as feed, not food, Jones said. “We have to think of feed mills like our farms; we need to increase feed-mill biosecurity.”
Today, feed should be part of an on-farm disease investigation, and within that lies a wide range of possible risk factors such as ingredients, vehicles and pests. But just like on farms, the biggest challenge involves people. Some of the same questions should be asked of both farm and mill workers:
Do they own pigs?Do they go to hog shows?What about the people they live and interact with?
People may unknowingly carry contaminated faecal, dirt or dust particles on their shoes or on clothing. For example, in a study that sampled worker boots for Enterobacteriaceae, which serves as a facility hygiene measure, revealed a 91 percent contamination rate.
Lines of separation
“Do employees changes shoes before entering the mill? The answer is always ‘no’,” Jones reported, adding that she sometimes even sees truck drivers clean the bottom of their shoes into ingredient pits. Not only is that a problem, but ideally, drivers should stay inside their trucks at all times. Mills should establish lines of separation and zoning to control personnel foot traffic; visitors should be accompanied and provided clean footwear, plastic boots or boot covers.
Perhaps the easiest and most basic protection measure is to place mats over receiving pits when not in use. Mud and sludge should be removed from trucks before reaching the receiving pit, with the pit remaining covered until the truck is ready to unload. Delivery vehicles also should be routed to avoid crossing roadways with ingredient trucks.
Keeping contaminants out of the mill environment and equipment is important because thoroughly cleaning and sanitising the conveying equipment, receiving pit or bucket elevators is nearly impossible. Using cones and funnelling devices can help limit spills during unloading.
Notably, spilled ingredients are commonly swept into the pit, which is another practice that needs to end. Many feed-manufacturing facilities have grain cleaners and dust-collection equipment in place to limit the risk of dust explosions. However, the collected material often is returned to the feed in order to reduce shrink, even though it’s been well established that dust and other screened particles can serve as carriers for biological hazards, including PEDv.
As a precaution in times of high pathogenic risk, Jones added that mill operators should consider sanitising trucks prior to entering receiving or load-out bays and establish Danish entry systems for workers and visitors.
The KSU feed-safety team has developed and posted a wealth of feed-safety and biosecurity resources online, including “strategies to impact biosecurity,” as well as videos addressing the specific areas of “receiving procedures,” “people and vehicles” and “ingredients.” There’s also a user-friendly feed-mill biosecurity audit form.
Refine testing options
Testing is necessary for a mill to monitor its pathogen risks and to better understand biosecurity breaches, but it’s not always welcomed with open arms.
“When you move into a feed mill, surveillance is complicated,” Jones said. “In part, because we’ve hit the limit of science - for now.” Questions remain as to: What kind of samples provide for a useful analysis? What pathogen should we look for? Where should samples be collected?
“One of our biggest limitations to understanding the risk that ingredients play in foreign animal disease entry is that the USDA does not allow testing for foreign animal diseases,” Jones added. “There is no validated method to collect or analyse a sample for any swine viruses, which has limited our research ability.”
Because mill operators already take random grab samples to evaluate ingredient specifications, the thought now is to use those to check for pathogen risks, if needed. However, that relies on the assumption that a contaminant is evenly distributed throughout the feed or ingredient, and that may not be the case.
Jones offered the example of a KSU study using recommendations from the Association of American Feed Control Officials Feed Inspector’s Manual to grab 10 probes of at least 5 kilograms from a 1-tonne ingredient tote. The researchers inoculated PEDv six times into soybean meal, loaded the meal into a tote and then took 10 grab samples for a total of 60. Half of each sample was used to make a composite sample, and the others were tested individually. She reported that only about one-third of the individual samples detected PEDv, while all of the composite samples were positive.
‘Time-consuming process’
“We found that if we mixed the samples, we were much more likely to detect the virus,” Jones said. “The problem is, this is a time-consuming process that is rarely done in the industry.”
Her recommendation is to apply environmental monitoring, akin to the rope test increasingly being used in hog facilities, to provide a more sensitive sample and a broader idea of pathogen presence. This also is not a new concept, as the human and pet food industries have used this method for more than a decade.
The KSU research team tested the risk that dust presents by contaminating an ingredient with PEDv and processing a batch of feed, then swabbed the equipment, walls, ceilings and so forth. “We found [PEDv] on ceilings and walls three floors away,” Jones relayed. “Wherever the dust settles, it’s contaminated.” And the virus stayed present even after four flushes with PEDv-negative feed.
“To decontaminate the facility, all equipment had to be disassembled and pressure washed with a 10 percent bleach solution,” she added, and that’s unlikely to occur in the real world.
The researchers also measured the infectivity of the dust, which did cause illness in pigs.
Fortunately, one of the best swabbing tools is a 4 inch by 4 inch pad of cotton gauze, something that’s inexpensive and readily available, Jones noted. Detailed guidance for environmental sampling is outlined on KSU’s feed website.
A word of caution is necessary when interpreting environmental test results. “Whenever we go from a liquid (virus) to a dry form (feed), we lose about 10 CT of virus,” Jones said, referring to the CT - or cycle threshold - results from a quantitative real-time polymerase chain reaction analysis. “Likewise, when we use an environmental sample, we lose another 3 to 4 CT.”
‘Walk it backward’
“You need to understand that you have to walk it backward for an accurate estimate of the potential contamination level if you’re relying on results in an ingredient or a swab,” she noted. For example, a PEDv-positive environmental result from a feed mill may be 13 or 14 CT higher than the actual pathogen present. “That has ramifications if the level is high enough to cause illness in an animal,” Jones said.
What to swab depends on what you’re looking for. Jones suggests swabbing exhaust fans, cyclones, dust collection systems, finished feed bins, receiving pits and workers’ shoes. “Those areas will give you a lot of information,” she said.
“If I’m concerned about ingredients, I’ll swab the inside of those bins instead of collecting a sample of the ingredient itself.”
Based on the CT results, it will tell her which ingredients or areas present the highest risk. At the same time, if she’s concerned about personnel, she’ll swab the floors to identify traffic patterns that need to be corrected.
Due to the lack of validated tests for swine viruses, Jones recommends using surrogate pathogens, like Enterobacteriaceae to at least determine hygiene and biosecurity risks within the mill. “It will be a lot faster and cheaper,” she added.
Although the feed sector is increasingly aware of and responsive to its role in preventing swine-pathogen exposure, there’s still a barrier to actual on-site testing of mills. This is largely driven by the fact that the FDA requires reporting within 24 hours if there’s a reasonable probability that the use of, or exposure to, a food article will cause serious adverse health consequences or death to humans or animals. However, Enterobacteriaceae contamination is not reportable, and the FDA is currently not enforcing swine viral contamination in feed mills, so it is an opportune time to understand the risk, Jones noted.
While there remain a lot of unknowns associated with feed, feed ingredients, milling processes and pathogen risk-mitigation strategies, progress is unfolding. With research leading the way, Jones and others have made finding answers a long-term priority.