From birth to bacon: the Croatian pig enterprise running its own supply chain
A large Croatian agricultural group has just introduced a new 1,350 sow herd to its already established range of livestock and grain farming enterprises.Owned and founded by Mirko Ervacic back in 1992, the Osatina group has grown with pace in its 26 years of existence: operating dairy farms, a pig fattening unit, a fruit and vegetable enterprise plus energy production.
The company started off as an agricultural pharmacy with three employees but is now a thriving multi-pronged business with 1,100 employees.
The Osatina Group is based at Semeljci just south east of Zagreb, and with a number of agricultural and horticultural operations, it is one of the biggest farms in Croatia.
It runs a pig fattening enterprise, established in 2006, finishing 20,000 pigs per year but has just introduced a herd of 1,350 sows to effectively double the fattening capacity to 40,000 pigs per year.
There are 1.121 million pigs in Croatia and as a net-importer of agri-food products, it imported €2.91 billion and exported €1.88 billion products in 2017 alone.
The goal for Croatia is to become more self-sufficient for food particularly for dairy, beef and pork meat. It is for this reason the Osatina group is expanding to supply its home market.
Osatina has two pig production locations and normally finishes 20,000 pigs per year but has recently added new facilities to house the 1,350 sows.
Owner Mirko Ervacic said: “We had production of over 20,000 pigs per year but with the introduction of our new sow herd we will increase capacity to fatten 40,000 pigs per year. We have two production locations and only use the Pietrain and Landrace breeds in our herd.”
Osatina used to source the majority of its pigs from a single breeding farm to ensure best practices of biosecurity and maintain a high herd health. However, by introducing its own sow herd, Osatina is increasing its herd health and subsequent biosecurity by having its own production system from birth to bacon.
Mirko said: “By introducing our own sows we can reduce our costs of production while at the same time increasing our quality. Our pigs will be produced from birth to bacon and that allows us to control the high quality through the entire system.
“The sows have their own new housing fitted out with the latest technology and a liquid feed system,” he said.
Osatina has used funds made available from the EU to finance the new pig housing and technology and has also invested in its staff to ensure they are well trained to look after the sows.
Mirko said: “Our team of technologists, veterinarians and nutritionists travelled to Denmark to learn all about pig production so that we will be well prepared for the new system of production.”
All animals in the dairy herd and in the pig herd are fed rations mixed on farm by Osatina’s own mill. By doing this the farm also ensures high herd health and controlled traceability of all feedstuffs.
Mirko said: “We mix our own rations designed by us using corn, barley, wheat, soy and oats as well as other raw ingredients.
“However, we do not currently have enough hectares of land on the farms for all of our required production of animal feed. On our land we produce corn and wheat for silage.
“We produce concentrated feed in our own feed mill specified according to formulations made by top nutritionists. We buy other animal feed ingredients from subcontractors and other external suppliers.
“Our mill has capacity to produce 100 tons of feed per day or 25,000 tons per year. We use around 40 to 50 per cent of that ourselves and the rest we sell on the open market.
“All the manure from the pigs is also stored in large slurry stores for around two to five months. After that time, we spread it on the land according to the EU Directives regulations that we must follow,” he said.
There are between 20 and 25 staff working at both the pig farm locations taking control of every step of production.
In terms of health issues, the Osatina pig herd is only affected by pneumonia caused by haemophilus parasuis and mycoplasma, according to the group.
Herd performance figures show the fattening pigs achieve a daily liveweight gain of 900 grams per day.
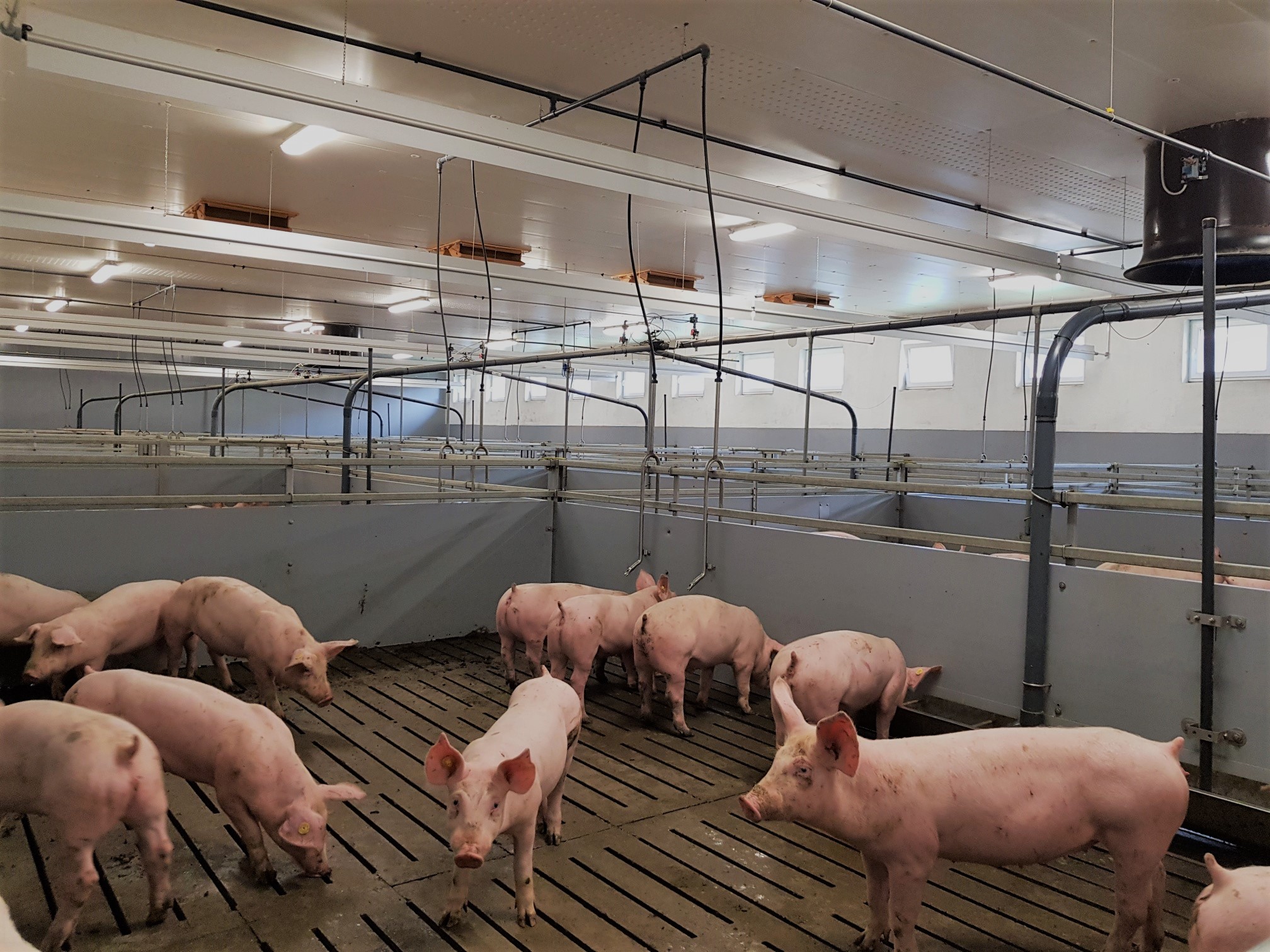
It takes around 110 days for the farm to finish the pigs to a carcass weight of 95kg with a 60 percent lean meat coverage.
“We have achieved a feed conversion rate of 2.90,” said Mirko. “When finished the pig sells for around €1.20 per kilogram or €145 per pig.”
Osatina operates its own biogas plants where it uses the slurry from the livestock to produce energy. The biogas plants were built with a capacity of 9 MW of electric energy (6.0 MW biogas and 3.0 natural gas) and 10.2 MW of heat energy. The plan is to expand, after which they would have a total of 15 MW of electric energy and 18 MW of heat energy.
Mirko said: “Slurry is used in biogas production. Guided by the experience of western European countries, we realised that the production of electricity from biomass is ecologically the most acceptable solution for managing the manure. We also use the energy in our greenhouses for the fruit and vegetable production and in the pig units,” he added.
Pig farming will remain a significant industry in Croatia as it consumes a high percentage of the cereals grown in the country and is a vital part of the agri-production chain.
Domestic pork production does not meet demand and in 2016 the country was importing up to 46 percent of its pork meat for consumers. Since then there has also been increased activity in importing live weaner pigs for fattening in Croatia.
While a new wave of Croatian consumers have extra income to purchase beef the demand for pork, meat is only expected to rise.
Words and photos Chris McCullough
Chris McCullough is a freelance multi-media journalist based in Northern Ireland and specialises in all aspects of agriculture. He has spent the past 15 years travelling the globe hunting for the best stories in food, farming and politics.