Heat Lamp Versus Heat Mat as Localised Heat Source in Pig Farrowing Crates
Research at Iowa State University reveals that savings can be made on heating costs by using heat mats rather than heat lamps for piglets in the farrowing room. Heating system did not affect piglet mortality or performance.Summary and Implications
Three, 40-crate farrowing rooms were selected for this comparison study. Half of each room used heat lamps for localised piglet heating while the other half of each room used heat mats. Sixteen turns over 12 months were monitored for power use, piglet mortality and average weight gain.
The only significant impact of either localised heating system was on the power use, where the mats were 36 per cent lower than the lamps.
Introduction
Swine farrowing operations face the unique challenge of maintaining two distinct thermal environments in the same facility. A sow and her piglets have very different thermal needs. Piglets require a dry, draught-free space at 32.2 to 35.0°C (90-95°F), while sows prefer a temperature of 15.5-18.3°C (60-65°F).
To meet these two needs, the room temperature is often kept in the 18.3-23.9°C (65-75°F) range and localised heating is provided to the piglets. There are two main methods of localised heating in the US swine industry - heat lamps and heat mats. There has been some work in the past examining the two heating systems.
Due to the current size of litters at weaning (around 10 per litter), a larger heated area may be needed to fit all the piglets.
The typical 0.3 metres by 1.2 metres (1ft by 4ft) heat mat might not provide enough area; hence 0.3 metres by 1.5 metres (1ft by 5ft) heat mats were used in this study.
The objective of this study was to quantify the effects of localised heating type–mat or lamp on piglet mortality, rate of gain, and electric power use in modern swine farrowing rooms.
Materials and Methods
For this study, three 40-crate farrowing rooms were equipped with 125-W heat lamps in half of the crates and 290-W 0.6 metres × 1.5 metres (2ft × 5ft) double heat mats shared between two crates in the other half of the crates (Figure 1).
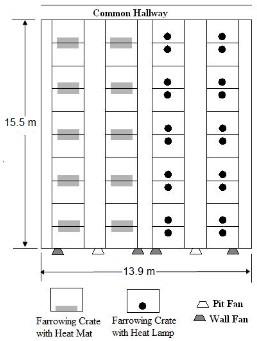
utilising heat mats and 20 crates utilising heat lamps (1m = 3.28ft)
A temperature-dependent, variable-output controller regulates the power supply to the mats. The lamps were controlled on/off by the room ventilation system controller and turned off when the room temperature exceeded the set point by 5.5°C (10ºF).
Electricity use of each half of the rooms was measured separately with electric meters and piglet performance was recorded by farm personnel and the research group.
Results and Discussion
The average weight gain (AWG) for piglets reared on heat mats versus heat lamps for the pre-weaning period is shown in Figure 2.
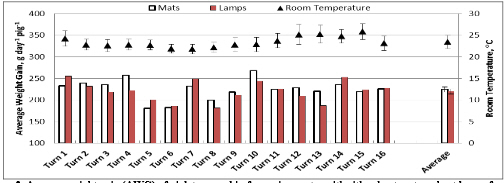
each farrowing turn, the overall AWG (±SE), and the average room temperature (±SD) for each turn (1lb=454g; °F = 1.8 × °C + 32)
There was no significant difference (P=0.63) between the two systems. The AWG (±SE) was 224g per day (±5.7) and 220g per day (±5.9) for the mat and lamps, respectively.
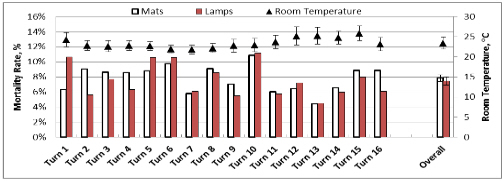
farrowing turn, the overall mortality rate (±SE), and the average room temperature (±SD) for each turn (°F = 1.8 × °C + 32)
Again, there was no significant difference (P=0.59) between the two systems. Overall, the pre-weaning piglet mortality (±SE) was 7.8 per cent (±0.4 per cent) with heat mats and 7.4 per cent (±0.5 per cent) with heat lamps. The turn-by-turn power use values are shown in Figure 4.
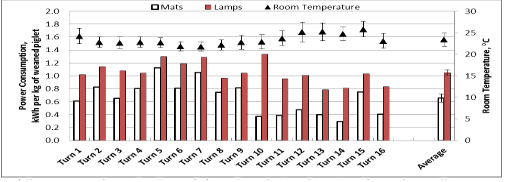
The cumulative power use per turn (±SE) was normalized to the specific mass of weaned piglets. The mats consumed an average of 0.66 (±0.06) kWh per kg (0.3 (±0.03) kWh per lb) weaned piglet while the lamps consumed 1.05 (±0.04) kWh per kg (0.48 (±0.02) kWh per lb) weaned piglet. This reduction was significant (P<0.0001) and resulted in a 36 per cent reduction in power use by the mats compared to the lamps.
With an assumed electricity rate of $0.07 per kWh, this represents a $0.026 per kg of weaned piglet or $0.14 per weaned piglet savings by the mats.
This study also included thermographical (IR) images of piglet usage of the mats and lamps. Analysis of these images is ongoing and will be published as a part of the final results of the project.
The authors of this paper - published in Iowa State University Animal Industry Report 2014 - were John Stinn (Graduate Research Assistant, Agricultural and Biosystems Engineering and Hongwei Xin (Professor, Agricultural and Biosystems Engineering and Animal Science).
Acknowledgements: The study was supported by a research grant from the Iowa Pork Producers Association and cooperation of the swine producer in allowing the researchers access to the production facility and animal production data.

Further Reading
You can see other papers in the Iowa State University Animal Industry Reports 2014 by clicking here.
May 2014